Porosity in Welding: Identifying Common Issues and Implementing Best Practices for Avoidance
Porosity in welding is a prevalent concern that typically goes unnoticed up until it triggers considerable troubles with the honesty of welds. In this discussion, we will discover the crucial aspects adding to porosity formation, analyze its damaging impacts on weld performance, and review the finest practices that can be embraced to decrease porosity incident in welding processes.
Common Sources Of Porosity
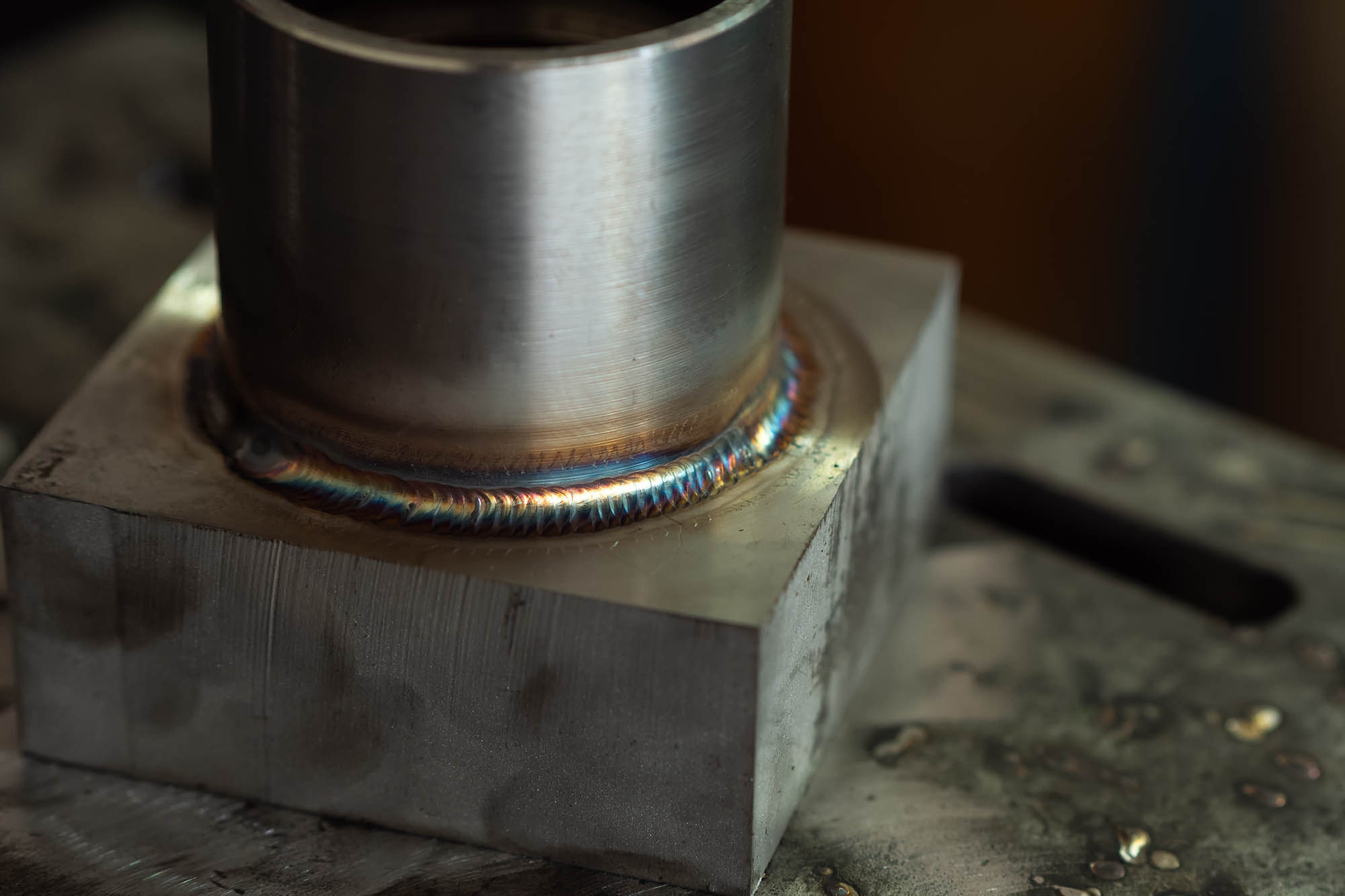
An additional frequent offender behind porosity is the visibility of impurities on the surface area of the base metal, such as oil, grease, or rust. When these contaminants are not efficiently gotten rid of prior to welding, they can evaporate and come to be caught in the weld, creating problems. Making use of filthy or wet filler products can introduce pollutants into the weld, contributing to porosity issues. To mitigate these common reasons for porosity, comprehensive cleansing of base steels, correct securing gas choice, and adherence to optimum welding specifications are important practices in accomplishing high-quality, porosity-free welds.
Influence of Porosity on Weld High Quality

The presence of porosity in welding can dramatically jeopardize the structural honesty and mechanical buildings of welded joints. Porosity creates gaps within the weld metal, compromising its total toughness and load-bearing capability. These spaces work as stress concentration factors, making the weld more vulnerable to fracturing and failure under applied lots. In addition, porosity can decrease the weld's resistance to corrosion and various other environmental elements, further diminishing its long life and performance.
Among the key effects of porosity is a reduction in the weld's ductility and strength. Welds with high porosity degrees have a tendency to display lower effect stamina and lowered capability to deform plastically prior to fracturing. This can be especially worrying in applications where check these guys out the welded elements are subjected to vibrant or cyclic loading conditions. Porosity can hinder the weld's ability to efficiently transfer forces, leading to early weld failing and potential safety and security threats in vital structures. What is Porosity.
Ideal Practices for Porosity Avoidance
To improve the architectural integrity and top quality of bonded joints, what certain actions can be applied to minimize the occurrence of porosity during the welding procedure? Utilizing the appropriate welding method for the particular webpage material being welded, such as readjusting the welding angle and gun placement, can additionally protect against porosity. Normal examination of welds and immediate removal of any type of problems recognized during the welding procedure are necessary practices to avoid porosity and generate premium welds.
Relevance of Appropriate Welding Techniques
Implementing correct welding methods is extremely important in making certain the structural integrity and quality of welded joints, developing upon the structure of reliable porosity prevention steps. Excessive heat can lead to raised porosity due to the entrapment of gases in the weld pool. Additionally, utilizing the browse this site ideal welding criteria, such as voltage, current, and take a trip speed, is important for accomplishing audio welds with very little porosity.
Additionally, the option of welding procedure, whether it be MIG, TIG, or stick welding, need to line up with the details demands of the job to make sure optimal outcomes. Proper cleansing and preparation of the base steel, in addition to choosing the ideal filler product, are also crucial elements of proficient welding strategies. By sticking to these best methods, welders can decrease the risk of porosity development and generate high-quality, structurally sound welds.
Examining and High Quality Control Procedures
Testing treatments are important to find and avoid porosity in welding, ensuring the stamina and durability of the last product. Non-destructive testing techniques such as ultrasonic screening, radiographic testing, and visual examination are frequently used to determine prospective problems like porosity.
Carrying out pre-weld and post-weld inspections is additionally important in preserving high quality control criteria. Pre-weld examinations entail verifying the products, devices setups, and tidiness of the work location to avoid contamination. Post-weld assessments, on the other hand, assess the final weld for any type of problems, consisting of porosity, and verify that it meets specified standards. Applying a detailed high quality control strategy that consists of comprehensive testing procedures and inspections is vital to minimizing porosity concerns and guaranteeing the general top quality of welded joints.
Verdict
To conclude, porosity in welding can be a common problem that affects the top quality of welds. By identifying the usual sources of porosity and carrying out finest practices for prevention, such as appropriate welding techniques and testing measures, welders can ensure premium quality and trustworthy welds. It is necessary to prioritize avoidance techniques to lessen the incident of porosity and keep the honesty of welded frameworks.
Comments on “What is Porosity in Welding: Key Variables and Their Influence On Weld Quality”